
Introduction
Caravan brakes are probably the least talked about – most important thing on a caravan. Most of the time we usually trust the caravan manufacturer, and take what they give us. The rest is handled by the caravan dealer, who usually organizes the car trailer plug wiring, and installs a brake controller in the car. They give a brief on how to use it, and what it does. And off we go to enjoy our first trip in our brand new caravan.
It is usually only when we encounter our first scary skid, sway or god forbid – a jack-knife, that we sit down and actually do some research on what the hell happened. It doesn’t take a college degree to figure out that the incident, probably had something to do with the brakes. Slamming on the brakes in a hairy situation is usually the what we would have been doing just before everything went south.
There are a lot of factors that are involved when considering towing a caravan safely. However being able to slow down or stop when the moment calls for it is probably the most important thing. Braking technology in automobiles has progressed a lot over the last few decades. Most new cars come standard with disc brakes and some sort of safety brake control feature like ABS (Anti-lock Braking System).
Caravan brake systems however, are still governed by cost rather than safety. Most manufacturers prefer the standard Electric Drum Brakes. They are easy to fit, low cos and easy to wire up and control. In this article we will be elaborating on various types of caravan brakes and the differences between them. But first we will look at the legal requirements for caravan brakes.
Caravan Brakes – Australian Laws and Regulations
All brakes that are fitted to trailers and caravans in Australia are required to comply with Australian Design Rules No. 38. The ADR’s in this section are mainly used by brake manufacturers to calculate appropriate braking forces required for various ratings. The most relevant rule to caravan manufacturers, and DIY modifiers is the classification of the trailers based on their weight and the type of braking required for each weight class. The Vehicle Standards Bulletin for Building Trailers specifies three distinct categories:
- Caravans and Trailers upto 750kg GTM – No brakes are required
- Caravans and Trailers from 750kg – 2000kg GTM – Brakes are compulsory on at least one axle. Over-ride brakes without the use of brake controller are permitted.
- Caravans and Trailers above 2000kg GTM – All axles need to have brakes. Breakaway braking systems are compulsory. Breakaway braking system as the name suggests engages the brakes automatically in the event of detachment of caravan from tow vehicle during travel. The breakaway system must be sufficiently charged enough to keep brakes engaged for upto 15 minutes from time of detachment.
Drum Brakes
The most standard of all caravan brake types the drum brake relies on friction of the braking shoes, on the inside of a drum to provide the stopping power. The entire braking assembly is housed in a cylindrical metal casing or drum.
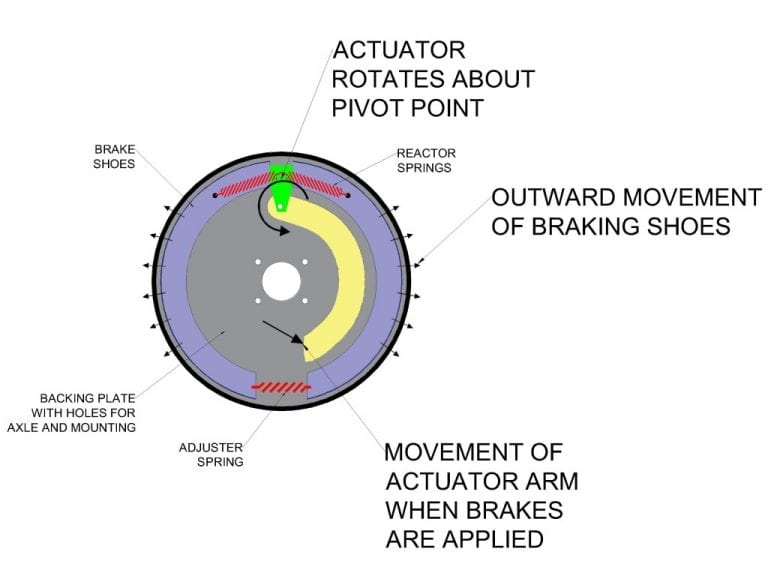
Fig. 1 Dynamics of a Trailer Drum Brake
A typical drum brake assembly consists of:
- Backing Plate – This forms the rear of the drum housing. The backing plate is can be called the foundation if the brake were a building. All the braking components except the drum are mounted to the backing plate. It is mounted to the fixed part of the axle and does not rotate with the axle. As a result The braking components mounted to the backing plate remain stationary with respect to the wheel as well.
- Brake Drum – The backing plate has a hole for the freely rotating axle to pass through, and connect to the front of the drum. The caravan wheels are connected to the front face of the drum. The rotating wheel – rotates the drum – which in turn rotates the axle.
- Brake Shoes and Lining- The brake shoes are usually made of cast steel or a similar alloy. They transfer the braking force to the drum by expanding against it. They also have a high friction lining that takes the brunt of the rubbing against the drum. If the lining deteriorates too much, you can hear the distinct “squeal” as a result of the metal to metal contact between the shoe and the drum.
- Actuator arm – This is the part of the brake that converts braking forces applied to it into the outward motion of the braking shoes. This rotates about a pivot and caused the brake shoes to move outward, and come into contact with the drum. Motion of the actuator arm is achieved via mechanical cables or by motion of electro-magnet in the case of electric brakes.
- Reactor Springs – These springs transfer the braking forces between the two shoes. The shoes forward to the direction of motion is called the leading shoe and the other is called the trailing shoe. The springs equalize the forces between to the leading an trailing shoe to ensure that the lining wear evenly.
- Adjuster spring – This spring is used to adjust the braking force required. By making the spring tighter or looser, the shoes can be bought closer to or farther away from the drum. This changes the braking response of the vehicle. The adjuster spring is usually set to a standard setting. Adjusting – the setting – if at all required – is only recommended to be done by qualified braking specialist.
Drum brakes are due to the following advantages:
- They are less expensive to make
- Easy to maintain and repair
- They allow easy incorporation of a parking handbrake via cables
- Because the shoes have a larger surface area compared to disc brake callipers, they face less wear for the equivalent amount of use.
- Being housed in a drum the braking components are less exposed to the elements and last longer.
The main disadvantage of drum brakes is the brake fade (reduction in braking force) caused due to over heating. The drum brakes rely on the efficient contact of the shoes with the inner surface of the drum. Over long periods of continuous use the brake drums can heat up quite significantly. This causes the drum to expand – and since it is circular the only way it expands is outward. This reduces the contact between the drum and the shoe, causing a reduction in braking. At high temperatures the properties of the brake shoe lining also change, causing less friction and hence less braking.
Depending on how the actuator arm is activated, there are two types of drum brakes.
Mechanical Drum Brakes
In mechanical drum brakes the actuator arm is made to move mechanically via steel cables. When pulled tight the steel cables cause the actuator to pivot and the braking shoes to engage the drum. Mechanical drum brakes are only used on trailers that weigh less than 200kg when fully loaded. The brakes are actuated via an over-ride coupling.
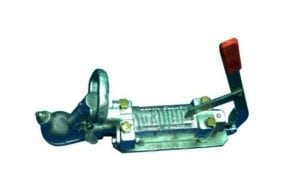
Fig 2. Mechanical Over-ride Coupling
When the towing vehicle brakes the coupling pushes against the ball attached to the vehicle. This moves the coupling in and out of a override cylinder. This motion tightens the cables causing the actuator arm within the drum to engage the brakes.
Electric Drum Brakes
Electric drum brakes are the stock standard brakes fitted to most caravans with loaded weight above 2000kg. By law they are required to be able to control the braking force form inside the tow vehicle. This is achieved via a braking controller mounted on the tow vehicle dash. The braking controller controls the current to the brakes and allows the tow vehicle brake pedal to talk to the caravan brakes via the trailer plug. Electric drum brakes are highly popular because of their quick braking response compared to the mechanical variant. The motion of the actuator arm is achieved by movement of an electromagnet attached to its end.
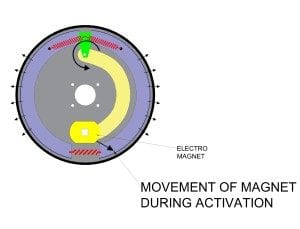
Fig 3. Electric Drum Brake
When the brakes are activated in the tow vehicle – an electric current is sent via the trailer plug to the electromagnet in the drums. The current charges the magnet and magnetizes it causing it to move outward towards the metal drum due to magnetic attraction. This in turn pivots the actuator arm which activates the brakes.
When a caravan travels offroad or over corrugations for long periods of time, the metal to metal connections within the drum brakes can face severe damage. Due to the constant rattling over one another the connection and joints can wear and damage over time greatly reducing braking efficiency. To overcome this brake manufacturers release off-road versions of their brakes with rubber bushings and grommets that prevent wear due to metal to metal contact and rattling.
Due to the fact that it uses electricity to initiate and control braking response, electric drum brakes are not used for marine and extreme off-road (creek crossing) applications.
Disc Brakes
Disc brakes have proven their performance – being widely used in the competitive motorsport since the 1950’s. Braking is achieved by using a calliper with pistons that pushes friction pads against a rotating disc attached to the wheel. The motion of the piston is achieved using hydraulic fluid such as the typical DOT brake fluids used in a car braking system.
A typical disc brake assembly consists of:
- Rotor- The disc component of the brake that rotates with the wheel is know as the rotor. For caravn brakes they are usually made out of cast iron, however high end rotors made of lighter cast alloys or ceramic composites can be used. The rotor is bolted to the wheels and rotates with it. The quality of the rotor’s surface is critical to braking. If too much rust develops, this can affect braking, and the rotors will need to be machined to make the surface smooth and straight again.
- Callipers and Brake Pads – The callipers house the braking pistons . The pistons on either side are fitted with friction or brake pads that come into contact with the rotating disc when the brakes are applied. The callipers are mounted to the fixed part of the axle and do not rotate with the wheel. The callipers can house one or more than one sets of pistons (usually referred to as “pots”) to achieve greater stopping force. Frictional material consisting of ceramic, Kevlar or other plastic based substances are used for brake pads. They suffer wear over time and can be replaced when they are beyond repair.
- Master Cylinder and Actuator – This is the master reservoir that contains the bulk of the hydraulic fluid used for braking. When the brake pedal is pressed the actuator is activated electronically or mechanically and works on the pistons in the master cylinder. The hydraulic fluid builds pressure in the master cylinder which due to laws of fluid dynamics exerts pressure on the pistons in the calliper. Since the pistons in the calliper have a smaller surface area than pistons in master cylinder, the amount of pressure exerted at the callipers is larger, and high braking force is achieved. Some disc brake systems such as the ALKO IQ7 use compressed air as an actuator to drive fluid in the callipers.
Disc brakes have many advantages over drum brakes:
- They have greater stopping power that drum brakes
- They have less moving parts and face less wear and tear. Hence they are widely used for offroad applications.
- Since the brake control at the wheels is hydraulic rather than electric they can be used for marine applications.
- They do not experience reduction in braking due to overheating like drum brakes.
- They recover better from wetting or immersion in water.
The main disadvantage with disc brakes is the cost. They are fairly expensive compared to a similar set of drum brakes. It is also more difficult to incorporate the parking handbrake, especially in electric over hydraulic brake types. Another problem is that the actuator usually requires some position to be mounted on the outside of the caravan. Drum brakes don’t have this hassle to deal with.
Mechanically Actuated Disc Brakes
Mechanically actuated disc brakes are actuated using a hydraulic over-ride coupling. Since braking cannot be independently controlled by the driver in the car, here again the maximum weight limit on the trailer or caravan is 2000kg.
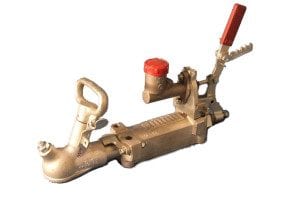
Fig 5. Hydraulic Over-ride Coupling
The master cylinder is located above the coupling. As the coupling moves in and out, the master cylinder piston is compressed and braking is achieved. The handbrake manually compressed the master cylinder to act as a parking brake when required.
Electric over Hydraulic Disc Brakes
These disc brakes are used on all trailers above 2000kg GTM. They can be controlled via dash-mounted brake controller similar to electric drum brakes. They have an actuator that converts the electric signal from the braking car into hydraulic response in the master cylinder. The actuator can come at ratings up to 1600PSI, for really strong braking power when needed. The ALKO iQ7 Offroad braking system uses compressed air to compress the hydraulic fluid during braking to achieve a better response. The compressed ait is maintained by an on-board compressor and is stored with the hydraulic fluid in a reservoir tank.